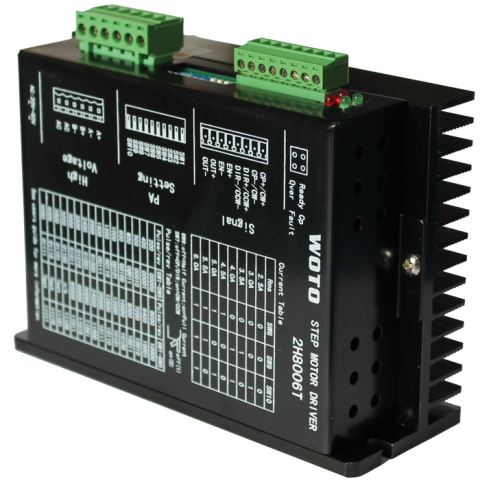


AC Stepper Motor Driver 2H8006T
-
Payment
-
Origin
China Mainland
-
Minimum Order
15
-
Packing
Pieces
- Contact Now Start Order
- Description
Product Detail
Characteristic :
1.Using new digital sinusoidal micro-segmentation algorithm
2.Support single / dual control pulse input
3.A test run function, power failure, phase memory function
4.Positioning accuracy, low noise, small temperature rise, high efficiency
5.Simple high-performance, multi-function, operation, cost-effective
6.With short circuit, overvoltage, undervoltage, overtemperature protection and improving functions
7.Motor parameters automatically adapt to the function to ensure maximum play all types of motor function
Stepper Motor Specification :
Input Power supply : | AC20V-60V 6A(MAX) |
Output Current | 2.5A-6.0A |
Drive Way | PWM(PWH) constant current chopping ,two phase Sine wave output current |
Suitable stepper motor | 60,85,86,110 series two phase stepper motor |
Ambient environment | -10?~55? 15~85%RH?No condensation. Non-corrosive, flammable, explosive, conductive gas, liquid and dust |
Keeping enviroment | -40?~+55?, <93%RH,No condensation, no frost |
Size (L*W*H) | 151X97X53 mm |
Net Weight | 0.7Kg |
Setting Current:
2H8006T | SW8-SW10 | 000 | 001 | 010 | 011 | 100 | 101 | 110 | 111 |
Current phase | 2.5A | 3.0A | 3.5A | 4.0A | 4.5A | 5.0A | 5.5A | 6.0A |
Setting Microstep selection:
SW1—SW5 | 00000 | 00001 | 00010 | 00011 | 00100 | 00101 | 00110 | 00111 | 01000 | 01001 |
Steps/rev | 200 | 400 | 500 | 600 | 800 | 1000 | 1200 | 1600 | 2000 | 2400 |
SW1—SW5 | 01010 | 01011 | 01100 | 01101 | 01110 | 01111 | 10000 | 10001 | 10010 | 10011 |
Steps/rev | 2500 | 3000 | 3200 | 3600 | 4000 | 5000 | 6000 | 6400 | 7200 | 8000 |
SW1—SW5 | 10100 | 10101 | 10110 | 10111 | 11000 | 11001 | 11010 | 11011 | ---- | 11111 |
Steps/rev | 10000 | 12000 | 12800 | 20000 | 24000 | 30000 | 40000 | 60000 | ---- | Tesp |
Description:
Microstep setting | Users can set the driver Microstep by the SW1-SW5 five switches,total 28 micro-step. When you set the microstep , pls stop the driver working?The setting of the specific Microstep subdivision, please refer to the instructions of the driver panel figure . |
Output current setting | Users can set the driver Microstep by the SW1-SW5 five switches. The setting of the specific Microstep subdivision, please refer to the instructions of the driver panel figure.. |
Double pulse setting | SW7 sets pulse mode, setting “on'' as double pulse mode, setting “off'' as pulse + direction mode.,CW+/CW is Clockwise ,CCW+/CCW- is Counterclockwise , need to confirm the wire of stepper motor ? |
Automatic half current function | Users can set the driver half flow function by SW6. "OFF" indicates the quiescent current is set to half of the dynamic current, that is to say, 0.5 seconds after the cessation of the pulse, current reduce to about half automatically. "ON" indicates the quiescent current and the dynamic current are the same. User can set SW6 to "OFF", in order to reduce motor and driver heating and improve reliability. |
Self test function | When SW1-SW5 is OFF , Inner of drive send 1K pulse to test whether the motor,wire,and self is normal? |
signal Interface | PUL+ and PUL- are the positive and negative side of control pulse signal; DIR+ and DIR- are the positive and negative side of direction signal; ENA+ and ENA- are the positive and negative side of enable signal . |
Motor Interface | A+ and A- are connected to a phase winding of motor; B+ and B- are connected to another phase winding of motor. If you need to backward, one of the phase windings can be reversed . |
Power Interface | It uses AC power supply,recommended working voltage is 20-60AC,power is over 200W,voltage shouldn’t be over 75AC and below 20AC? |
Indicator Lightor | There are two indicator lights. Power indicator is green. When the driver power on, the green light will always be lit. Fault indicator is red, when there is over-voltage or over-current fault, the red light will always be lit; after the driver fault is cleared, if re-power the red light will be off.? |
Installation | The size of motor driver is 151×97×53mm,mounting holes is 139mm?Chest and upright installation are ok,we suggest upright installation? During installation, it should be close to the metal cabinet for heat dissipation. |
signal interface and sequence in time :
Inner electric circuit of motor drive :
Connection of Output alarm :
??:OUT?????OC??,??????30VDC,??????100mA ???
?????,????????
Note : OC is output of photoelectric isolation , Max voltage capability is 30VDC ,maximum saturation current is 100 MA motor driver .
Output optocoupler is not conducted under the normal working condition .
Interface connection and instation :
- High Torque Nema 23 Stepper Motor 425 Oz In 1 Pieces / (Min. Order)
- Nema 23 Stepper Motor 1.26N.m 1 Pieces / (Min. Order)
- Nema 23 Stepper Motor 1.89N.m 1 Pieces / (Min. Order)
- 110V Stepper Motor Driver 2H1106T 1 Pieces / (Min. Order)
- 220V Nema 34 Stepper Motor Driver 2H2208T 1 Pieces / (Min. Order)
- Brushless Motor Driver 15 Pieces / (Min. Order)
- 2000W Servo Motor Drivers 15 Pieces / (Min. Order)
- 1500W Servo Motor Driver 15 Pieces / (Min. Order)
- Driver Stepper Motor 2H606T 15 Pieces / (Min. Order)
- Three Phase Motor Driver MD-3008B 15 Pieces / (Min. Order)
- Nema 52 Stepper Motor Driver 3008A 15 Pieces / (Min. Order)
- Low Voltage Motor Driver 3DM683 15 Pieces / (Min. Order)
- Motor Driver For Nema 2M423A 15 Pieces / (Min. Order)
- Small Stepper Motor Driver 2M422A 15 Pieces / (Min. Order)
- 220V Motor Driver 2H2208T 15 Pieces / (Min. Order)
- Motor Driver 2H1106T 15 Pieces / (Min. Order)
- 1.2 Degree Nema 52 Stepper Motor 1303P 15 Pieces / (Min. Order)
- 1.8 Degree Nema 52 Stepper Motor 130STH 15 Pieces / (Min. Order)
- Nema 42 Stepper Motor Round Shape 1103P 15 Pieces / (Min. Order)